真空成形(真空成型)・圧空成形(圧空成型)の
素材・型・
メリットデメリット
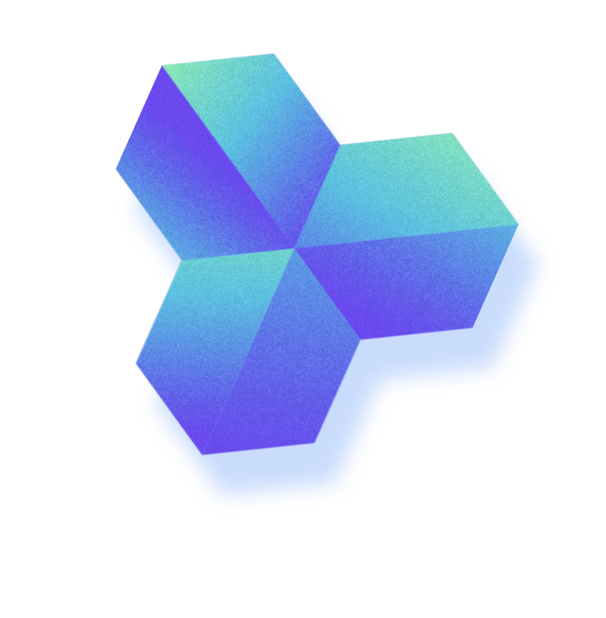
知っておきたい
真空成形(真空成型)・圧空成形(圧空成型)のポイント
製品の形状やデザイン、使用する材質、コスト、品質など、成形法や使用する型を選ぶときの基準は様々。
ここでは、代表的な成形方法である真空成形・圧空成形に関する選び方のポイントをQ&Aでまとめてみました。
Q
真空成形・圧空成形は、どんな材料に対応できますか?
使用可能な材質はABS・AES・アクリル変性塩ビ(カイダック、タフビロン)・PMMA・PC・PP・PE・HIPS・PET・PVCなどが一般的ですが、軟質・硬質・発泡シート・不織布など種類の異なった材料を複合した「複合多層材
料」や「シルクスクリーン印刷された材料」も使用できます。
またPEI・PSF・PEEKなどのスーパーエンプラ材料の成形も可能です。

材料事例

Q
真空・圧空成形では、どんな型を使用しますか?
試作段階では木型か人口木型、量産では樹脂型または金型を用います。
また、それぞれに凹型凸型の2種類があり、製品の特徴に合わせてどちらか一方の型を使用します。

型の種類について
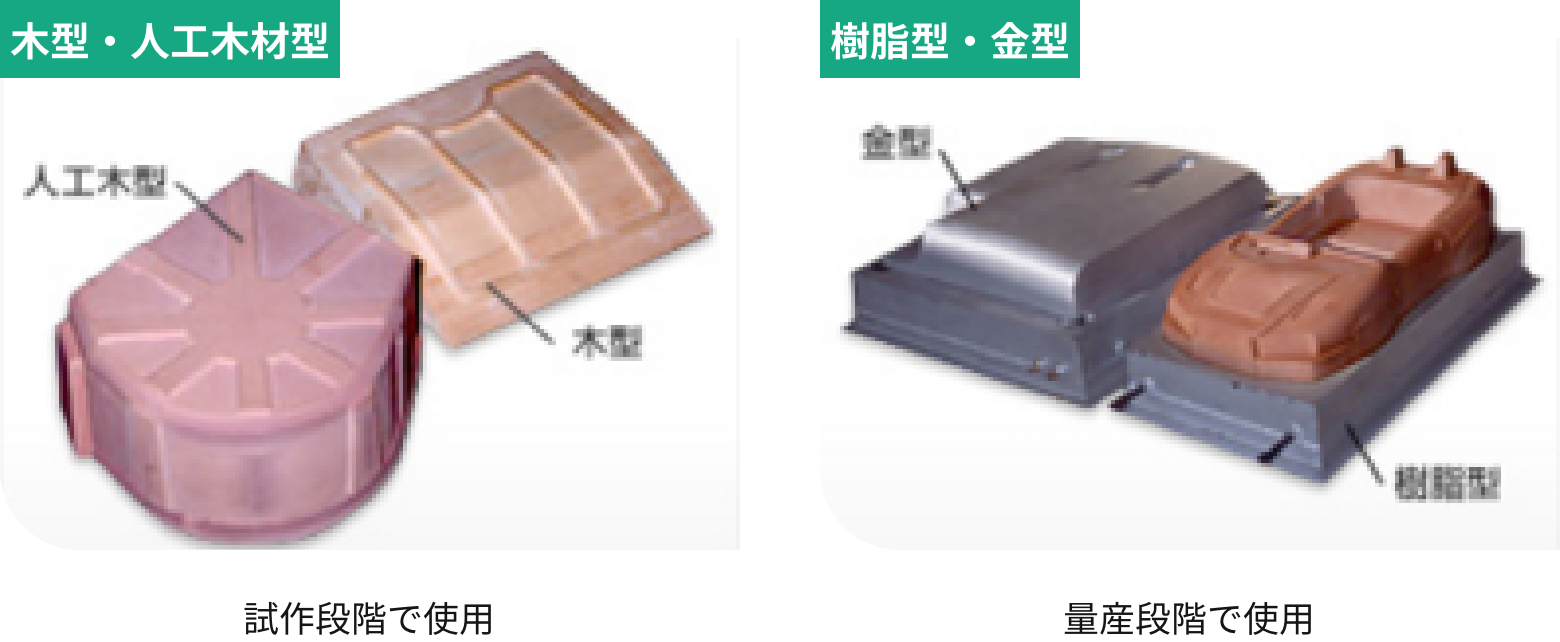

凸型・凹型の特徴
凸型の特徴
・成形品内側の寸法を正確に出したい
・成形品中央部の肉厚を大きくしたい
・成形品全体の肉厚をできるだけ均一にしたい
・複合多層材料を成形する場合
(印刷シート・メタリックシート・布張合せシート)
・型費用を低減したい
凹型の特徴
・成形品外側の寸法を正確に出したい
・成形品外側のデザインをシャープに出したい
・商品のデザイン自体が深絞りで、プラグアシストが必要な場合
Q
型の材料の選び方を教えてください。
作りたい製品の形状や精度、コスト等によって変わります。
それぞれの長所や短所は以下の表をご参照ください。

型の種類について
試作用 | 量産用 | |||
---|---|---|---|---|
木型 | 樹脂(人工木材) | 樹脂型 | 金型 | |
長所 | 材料費、加工費が安い 製作日数が短い |
材料費、加工費が安い 製作日数が短い |
試作木型をマスター型に 使用できる 製作日数が短い |
強度・耐久性が良い 表面状態が良い 型の温度調整が可能でソリの少ない成形品を製作できる |
短所 | 表面状態が悪い ヒビ割れ、継ぎ目の 開きがでる 成形品に木目が転写される 熱伝導率が悪く冷却に 時間が掛かる |
ヒビ割れは発生しにくいが、 膨張するため、 寸法安定性が悪くなる 熱伝導率が悪く 冷却に時間が掛かる |
熱伝導率が悪く冷却に 時間が掛かる 型の温度調整が出来ないため、 多少のソリが発生する シャープな形状には不向き |
樹脂型と比べ価格がやや割高 |
耐用 | 数ショット | 数~数十ショット | 量産可能 数千~数万ショット |
量産可能 数万ショット以上 |
材質 | 紅松 姫小松 |
エボキシ | エボキシ ポリエステル |
AL ZAS |
Q
真空成形・圧空成形のメリットとデメリットは?
試作段階では木型か人口木型、量産では樹脂型または金型を用います。
また、それぞれに凹型凸型の2種類があり、製品の特徴に合わせてどちらか一方の型を使用します。

メリット
型費が安い
射出成形型の1/6~1/10程度。
製品サイズが大きいほど割安。
金型製作期間が短い
ほとんどの場合30日以内で可能。
凹凸とちらでも
凹型と凸型のどちらでも成形可能。
部分的なデザイン変更が容易
型改造が容易で、穴位置や
切り欠きの変更等は型改造不要。
大型サイズの製品ができる
1500mm×2500mm
深さ凸型620mm
凹型720mmまで可能。
小ロット生産が可能
数個の試作レベルから量産まで可能。
材料厚みの自由度が高く
薄いものから厚いものまで対応。
複合多層材料の成形が可能
軟質・硬質・発泡シート・不織布など
異なる種類の材料を複合した
成形が可能。
多彩なシートに対応
印刷シート、機能性シート、
加飾シートの成形が可能。

デメリット
ボスを付けることができない
後加工・接着等になる。
製品代が高い
(単発成形の場合のみ・薄肉連続成形は割安)
射出成形と異なり、一度シート状に押出した材料を二次成形するため、製品コストが高くなる。
後加工が必ず必要になる
不要な部分のトリミングが必要。
製品1ヶのサイクルタイムが長い
(単発成形の場合のみ)
連続成形や射出成形と比較し、単発成形の場合のみサイクルタイムが長い。
部分的に肉厚が変動する
コーナー部分の肉厚が薄くなりやすい。
寸法精度にバラツキが生じる
型に当たらない面の寸法精度にバラツキが生じる。